World’s highest on-site 3D printed bunker built in Leh at 11,000 ft by IIT Hyderabad, Simpliforge
IIT Hyderabad, Simpliforge 3D print world’s highest military bunker at 11,000 ft in Leh
By Newsmeter Network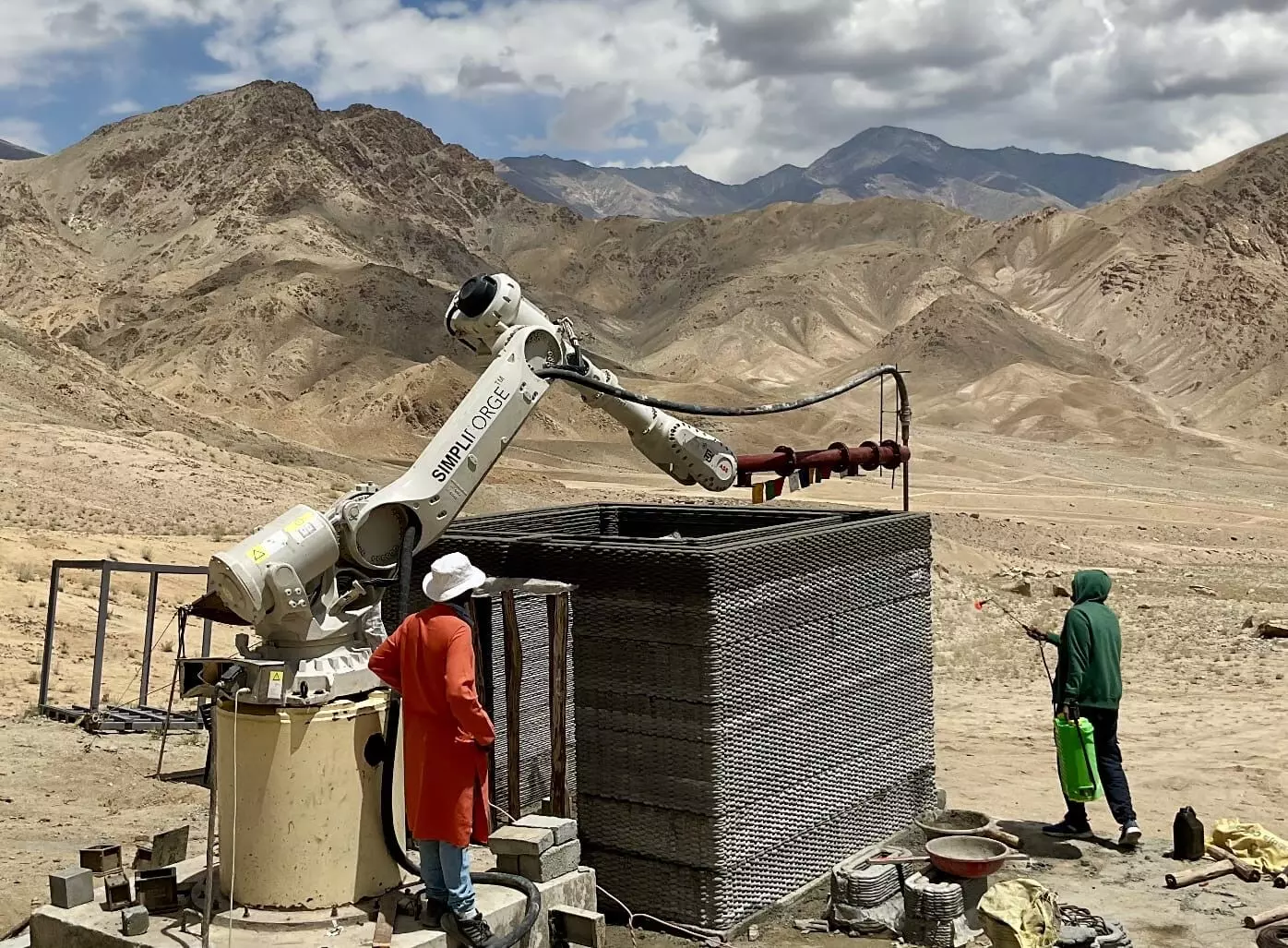
Leh: IIT Hyderabad, Simpliforge 3D print world’s highest military bunker at 11,000 ft
Hyderabad: In a boost to the country’s military industrial complex, Simpliforge Creations and IIT Hyderabad, in collaboration with the Indian Army, have successfully accomplished the world’s highest on-site 3D construction printing of a military structure at 11,000 feet above sea level in Leh.
3D printing in extreme environment
Professor KVL Subramaniam of IIT-Hyderabad and the team, along with Simpliforge Creations, developed specialised 3D printing technology capable of operating under extreme environmental conditions.
This innovation enabled the construction of a form-optimised protective bunker using locally sourced materials, completed over a total printing time of 14 hours.
Technology and academic collaboration
The Prabal initiative showcased how homegrown technology and academic-industry collaboration can push the boundaries of construction science. The deployment of this 3D printed bunker is not only a first-of-its-kind in India but also sets the stage for rapid, on-site, deployable infrastructure in challenging terrains, further strengthening the country’s defence preparedness.
This groundbreaking project marks a convergence of engineering innovation, military utility and the Make-in-India spirit—paving the way for future-forward infrastructure solutions, a public announcement from the team said.
Simpliforge Creations CEO Dhruv Gandhi said, “Executing this project in the high-altitude, low-oxygen environment of Ladakh was an immense operational challenge for both our team and our machines. The robotic printer system was set up and commissioned in under 24 hours, proving its agility and mobility. The reduced oxygen levels affected everything from power systems performance, which were delivering lower energy output than they would on normal plains, to human efficiency. The low humidity and high UV posed challenges to the integrity of the built material. Despite these constraints, we were able to meet our production targets and deliver a robust structure within a record timeframe of 5 days.”
Using engineered materials in printing
Prof KVL Subramaniam of IIT Hyderabad said, “One of the most critical aspects of this project was the development of specially engineered materials tailored to perform in extreme environmental conditions. Operating at high altitudes with low oxygen levels, low humidity and significant thermal variations required not just structural innovation, but also material science at its finest. Our team at IIT Hyderabad, in collaboration with Simpliforge Creations, designed a concrete mix that could be 3D printed on-site while offering superior mechanical performance, durability, and resilience. Before deployment, we conducted vigorous testing at IIT Hyderabad’s advanced facilities, including comprehensive studies on local sand and aggregates sourced from the region, and rheology of the mix. Understanding the material behaviour under simulated environmental stresses allowed us to optimise the mix design for on-site usage. This material innovation was fundamental to achieving the desired strength and structural integrity within such a challenging context.”
Arun Krishnan commented, “Project Prabal was conceptualised and initiated during my MTech program at the Indian Institute of Technology Hyderabad. Several teams and companies had attempted to bring 3D printed construction to the high-altitude terrain of Leh, but the extreme conditions of Ladakh proved to be a formidable challenge. It was the unmatched synergy between Simpliforge Creations and IIT Hyderabad that finally made it possible. Their technical depth, adaptability and relentless focus on innovation enabled the successful execution of Project Prabal. Together, we didn’t just build a structure—we proved that indigenous, cutting-edge technology can overcome even the harshest operational environments and deliver tangible impact for our armed forces. The printed structure has undergone rigorous trials.”
3D technology for building bridges and places of worship
Hari Krishna Jeedipalli, MD of Simpliforge Creations, said, “We’ve been pushing the boundaries of additive construction since 2022—from building India’s first 3D printed bridge to the world’s first 3D printed place of worship—and the Indian Army’s first in-situ 3D printed medical facility using locally available material. Each project has been a leap forward, and this bunker in Ladakh marks a crucial milestone in our journey towards extra-terrestrial”.
“Looking ahead, we envision commercialising this technology for remote terrain applications and extending this beyond Earth, towards space habitats on the Moon and Mars. Printing in the extreme, open conditions of Ladakh has given us vital insights and validation for operating in these types of terrestrial environments. It’s more than construction—this is a stepping stone on our journey into space deep tech,” added Hari.