What caused explosion at Sigachi Industries? Here are some probable factors
Over 30 lives were lost after an explosion ripped through Sigachi Industries’ pharma unit near Hyderabad on Monday
By Sistla Dakshina Murthy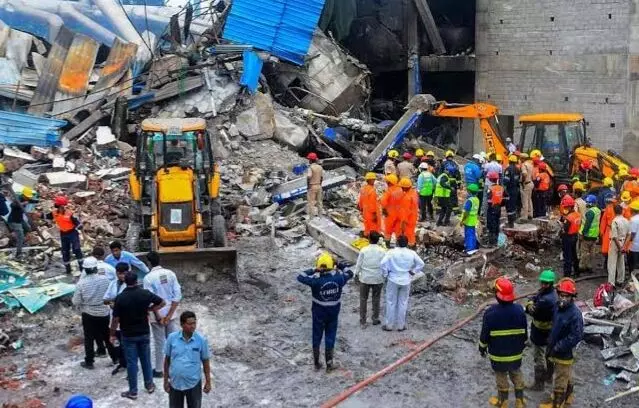
What caused explosion at Sigachi Industries? Here are some probable factors
Hyderabad: Preliminary investigation into Sigachi Industries’ explosion has indicated a series of operational, mechanical, and systemic failures.
Over 30 lives were lost after an explosion ripped through Sigachi Industries’ pharma unit near Hyderabad on Monday.
Here are 10 probable factors, according to safety experts, that may have led to the state’s worst industrial disaster:
1. Failure to maintain the blow Air Handler
Experts suspect that irregular cleaning of the blow air handler disrupted airflow regulation, causing temperatures in the spray dryer to rise uncontrollably.
2. Excessive temperature buildup in the Spray Dryer
The temperature reportedly shot up to 700-800°C, far above normal operating levels, indicating either a sensor failure or negligence in monitoring.
#Hyderabad--Massive blast at Sigachi Pharma unit kills over 30 workersDeath toll in the #SigachiPharma Industries explosion rises to 37. At least 35 injured, 11 critical.Search on for 27 missing workers.District Collector P Pravinya said that toll may rise further.… pic.twitter.com/FA26B9pJKR
— NewsMeter (@NewsMeter_In) July 1, 2025
3. Non-Functioning Safety Alarms or Sensors
Temperature sensors or alarms may have been defective or ignored, preventing timely intervention before reaching dangerous heat levels.
4. Dust accumulation in Dryer Chamber
Microcrystalline Cellulose (MCC) powder is combustible. Dust deposits within the dryer could have ignited under high heat, triggering an explosion.
5. Deviation from Standard Operating Procedures (SOPs)
There are indications that SOPs for cleaning, cooling, and temperature regulation were not rigorously followed, compromising safety.
6. Inadequate Preventive Maintenance Checks
Routine mechanical inspections and preventive maintenance might have been skipped or inadequately conducted, leading to system failures.
7. Ageing Equipment with No Upgradation
Operating for over four decades, the factory’s machinery, including the spray dryer, may have become obsolete or unsafe without timely upgrades.
8. Lack of Skilled Safety Personnel
Absence of technically trained personnel capable of immediately identifying process hazards or abnormalities could have worsened the crisis.
9. Weak Internal Safety Audit Mechanisms
The blast indicates possible gaps in internal audits and risk assessments, allowing critical faults to remain unaddressed.
10. Inadequate Emergency Preparedness
The scale of fatalities and injuries suggests poor evacuation planning and emergency response training, leading to high casualties.
According to safety experts, this tragic incident underlined the critical need for rigorous maintenance, real-time monitoring, and strict adherence to industrial safety protocols when operating high-risk equipment like spray dryers.
Detailed forensic and regulatory investigations will establish accountability and pave the way for stricter safety standards in Telangana’s industrial landscape.